With so many technologies communicating wirelessly, it makes sense to investigate whether wireless current transformers are practical for industrial or commercial applications. Could wireless CTs revolutionize the industry? The following is a list of four key considerations for deciding between wired or wireless CTs: Accuracy, Installation, Flexibility, and Price.
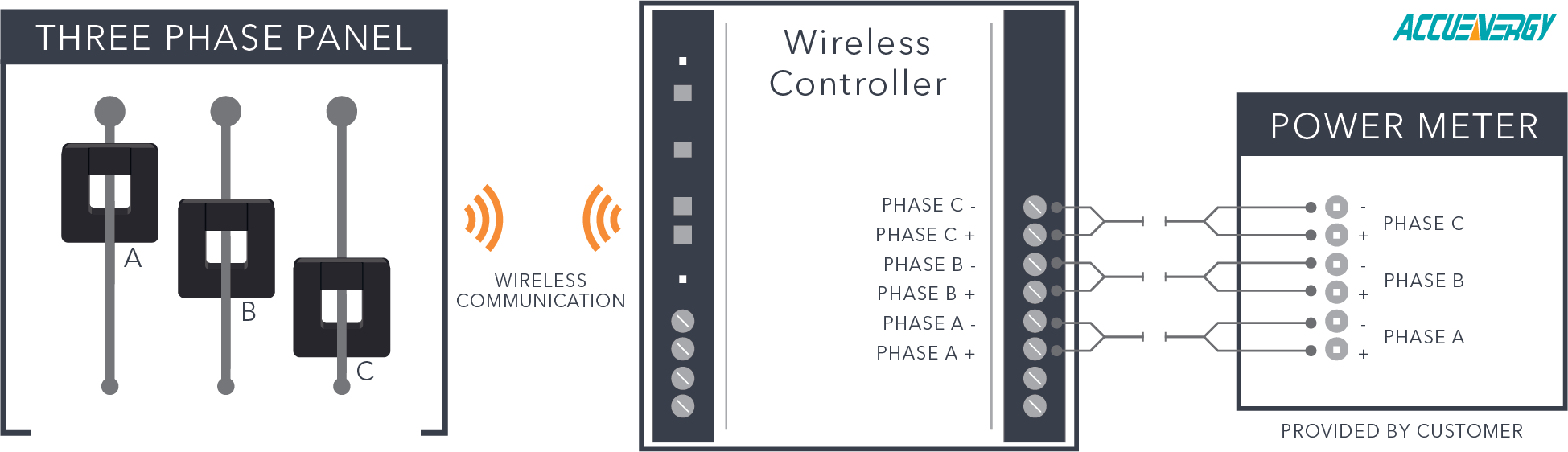
Accuracy
In order for a power meter to accurately measure an electrical service, it is critical to take careful readings of the voltage and current references as well as an exact frequency measurement. If any of these measurements are inaccurate, the final energy measurement will be skewed, resulting in unreliable data.
In a system reliant on wireless CTs, current measurements are transmitted wirelessly to a receiver which is then connected to a power meter. The wireless transmission of data can impact the frequency measurement or shift the frequency measurement between voltage and current.
Interference can also have a negative impact on current measurement accuracy. There are many sources of interference in and around an electrical panel. Wireless transmissions are inherently susceptible to wireless interference and, in the case of wireless CTs, this can cause readings to be missed for a cycle or even longer, depending on severity.
While it may be possible to compensate for distorted readings, accuracy is always negatively affected. Ultimately, wireless CTs tested under ideal conditions typically meet the 1% accuracy class.
In contrast, wired CTs can deliver highly accurate measurements in a broad range of applications and conditions. Current is still directly sensed by the transformer and sent to the energy meter. However, the signal is transmitted via a direct, wired connection (typically over twisted pair wire) producing proper frequency measurement between voltage and current. In this scenario, there are no missed readings due to interference from wireless signals. In fact, the twisted pair wire helps to maintain signal fidelity.
Proven for decades, accuracy of wired CTs is trusted and repeatable. The best wired CTs on the market today can produce 0.5% accuracy or better and are typically referred to as measuring at “revenue grade” accuracy.
Installation
Wireless and wired CTs share a similar installation process in an electrical panel. In both instances, an electrical panel must be accessed by a trained, licensed professional and the CTs must be installed around the appropriate conductors with a careful eye on orientation. For wired CTs, the next step in the installation is running the lead wire from the CTs out of the electrical panel in preparation for meter connection. This step is bypassed for wireless CTs and replaced by configuring wireless connectivity.
While the installation itself may be fairly quick for either configuration, it is important to note that considerable time may be needed to set up the wireless connectivity of wireless CTs to ensure a stable connection to the receiving module. Additional troubleshooting may be required in noisy environments where a reliable connection can be difficult to maintain.
Post-installation, unreliable wireless connections can lead to system downtime, loss of valuable energy data, or an increase in expensive on-site service calls. Ongoing system maintenance, including hardware replacements, connectivity checks, and battery changes are also essential in nearly all cases.
It is also important to note that, while the CTs themselves may be considered “wireless,” the rest of the system will rely on wires. For example, the controller/receiver will need to be wired to a power meter. The power meter itself will also need a wired connection to the voltage in the electrical panel. The electrical panel will need to be de-energized prior to installation and, therefore, a shutdown is unavoidable no matter which CT type is chosen.
When these factors are considered, there is very little time saved when comparing a wireless CT to its wired counterpart. In fact, wireless CTs may take additional time, considering communication troubleshooting and ongoing maintenance, which are typically unnecessary for wired CTs.
Flexibility
Since wireless CTs are the relative newcomer in the energy monitoring marketplace, the amperage range options continue to be limited and, in many cases, are designed to monitor relatively small loads (up to 200 amps). This severely restricts the range of projects that they can be used on. In an attempt to extend the measurement range, a third-party patch solution can be utilized, but unfortunately this can lead to further costs and introduce additional error into an already error-prone system. In some instances, a whole new meter must be selected to help compensate for the CTs shortcomings, adding even more cost and complexity to the project.
In contrast, wired CTs offer a robust design and a wide selection range of current ranges (up to 50,000 amps) to satisfy nearly any project requirement in a range of applications from residential to commercial or industrial. A variety of form factors, from hinged split cores to Rogowski coils, can meet even the most demanding installations.
Price
Although a single wireless CT may be priced nearly the same as a comparable wired model, the cost of the current sensor receiver module must also be considered. When the receiver is factored in, the overall cost can be double that of a wired CT.
Additionally, the cost of a metering system is more than just the price of the hardware itself. Installation and troubleshooting time also need to be examined as it affects the overall cost of the project. These invisible costs can add up quickly, especially in challenging installation environments.
In the end, wireless CTs may simply be out of reach for price-sensitive projects or high-volume applications.
Conclusion
When wired and wireless CTs are compared across accuracy, installation, flexibility, and price, it becomes clear why wired CTs remain the industry standard for energy management. While the concept of wireless CTs may seem attractive on the surface, the reality is that they remain impractical for rigorous applications that require stringent accuracy and dependable service. For these reasons, wireless CTs are not yet used widely throughout the energy management industry.
Accuenergy has over 20 years of experience manufacturing power meters and current transformers. While wireless CTs have been researched, the technology’s fundamental disadvantages prevent it from being a viable solution in the marketplace.
For installations that could benefit from a wireless option, Accuenergy recommends utilizing standard, wired CTs and metering hardware equipped with built-in wireless communication, such as WiFi. Where a wireless network is unavailable, consider an Ethernet connection to a network to communicate metering data to a building management system (BMS).
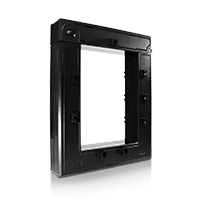
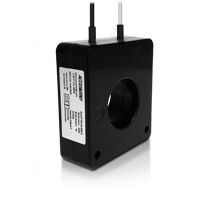